At Novatech, the main business activities cover high-tech industry processing supply system engineering, project contracting, and equipment manufacturing and installation, as well as environmental protection and green energy equipment manufacturing, sales, installation, and testing. The safety of products and services is the core of our business operations. The Company strives to ensure the safety of customers and employees during the installation or operation of equipment to avoid casualties, property losses, and violations of related safety regulations. To achieve this goal, we introduced the OHSAS 18001 Occupational Health and Safety Management System first in 2016. After the International Organization for Standardization (ISO) released ISO 45001 Occupational Health and Safety Management System on March 12 2018, we actively promoted the transition from OHSAS 18001 to ISO 45001 and obtained the ISO 45001 certification in 2019. We have the "Work Health and Safety Policy" and related procedures and standards drawn up according to ISO 45001 and implement environment, health and safety (EHS) management systematically based on the plan-docheck-act (PDCA) cycle.
Management Approach
Disclosure | Novatech's Practices |
---|---|
Importance | Maintain the environment, health and safety of customers and employees and mitigate the risk of industrial accidents with the safety of products and services as our top priority. |
Management strategies |
Comply with EHS regulations and customer requirements, increase employees' awareness of environmental safety through training, and implement continuous monitoring, prevention and correction mechanisms |
Policies/ commitments | Quality and EHS Policy |
Goals and targets |
|
Responsibility | Occupational Safety and Health Committee and ISEP Department |
Resources | SEP Department |
Grievance mechanisms |
|
Action plans |
|
Effectiveness assessment |
|
Occupational Safety and Health Management Policy
Comply with EHS regulations and customer requirements
Increase employees' awareness of quality and environmental safety through training
mplement continuous monitoring, prevention and correction mechanisms
Achievements in Occupational Safety and Health Management | |||
---|---|---|---|
Policy | Goal | Achievements in 2019 | Progress |
Comply with EHS regulations and customer requirements | Less than one ticket for violation of customer requirements per month and less than 12 per year | Four tickets for violation of customer requirements | Achieved, with improvement made by all units in charge |
Implement continuous monitoring, prevention and correction mechanisms |
|
49 tickets for contractors' violation of industrial safety regulations | Achieved, with improvement made by all units in charge |
Increase employees' awareness of quality and environmental safety through training | Conduct drills in emergency response planning for chemical accidents | No participants in drills in emergency response planning for chemical accidents | No drills in emergency response planning for chemical leaks were organized as no large chemical projects were undertaken in 2019. |
Increase employees' awareness of quality and environmental safety through training | 100% execution of internal training programs |
|
Achieved Note: Training on acid discharge/pipeline dismantling held once every two years was held in 2018. |
Comply with EHS regulations and customer requirements | Zero occupational accidents | A total of 1,622,978 accident-free hours were accumulated as of December 2019 | Achieved |
2020 Occupational Safety and Health Management Goals
Goal
Action plans
Zero Occupational Accidents
- Maintain zero industrial accidents (employees)
- Maintain zero industrial accidents (contractors)
Tickets for Workplace Safety Violations
- Receive less than 12 tickets for violation of customer requirements per year (passive indicator)
- Identify more than 36 defects in independent industrial safety management or tickets for violation of industrial safety regulations per year (active indicator)
Internal Training
- Communicate construction safety and health regulations to new contractors
- Organize training on high-risk operations (increasing the awareness of chemical hazards and wipe disposal, hazards associated with confined spaces, and acid discharge/pipeline dismantling)
Occupational Safety and Health Committee
Novatech has established the Occupational Safety and Health Committee according to law. The Occupational Safety and Health Committee convenes on a quarter basis. In 2019, the Occupational Safety and Health Committee consisted of nine members, including President as the chairperson and six members as labor representatives (66.67% of the total members). Upholding the spirit of continuous improvement in EHS management, the Occupational Safety and Health Committee convenes on a regular basis to discuss occupational safety and health issues, review the results of EHS activities and management, and oversee and float related occupational safety and health plans. In an annual staff meeting held at the end of each year, the ISEP Department presents the results of environmental and occupational safety and health management and related cases to demonstrate its efforts to contribute to a safe and healthy workplace that is free of accidents. We expect each of our employees to abide by the workplace safety and health policy and work together to mitigate potential EHS risks.
Year | Number of committee members | Number of labor representatives | Number of employees | Percentage of labor representatives (%) |
---|---|---|---|---|
2017 | 9 | 7 | 141 | 77% |
2018 | 9 | 7 | 160 | 77% |
2019 | 9 | 6 | 157 | 67% |
Disaster Response and Emergency Drills
Novatech attaches great importance to the health and safety of employees and is committed to building a safe and healthy workplace. We regularly hold training and drills for various types of disasters at the operations according to the established "Emergency Preparation and Response Procedures" to make sure that emergency response drills are effective. This enables our employees to better adapt to accidents, so as to avoid or reduce casualties, property losses, and environmental impacts. At Novatech, the "Work Safety Day" is set on March 30. We require in the orientation program that new employees should take safety and health training courses; all employees are also required to attend safety training courses on a regular basis to keep abreast of the amendments to related EHS regulations and news about industrial accidents in the past year. As to fire safety, we organize the fire safety training and evacuation drill twice every year to familiarize employees with evacuation routes and refuge points and related fire safety knowledge. In point of chemical leaks, we hold the emergency response drill for chemical leaks at the operations before chemicals are tested to familiarize operators with protective gear and necessary measures to be taken in case of emergencies.
Fire Safety Training in 2019
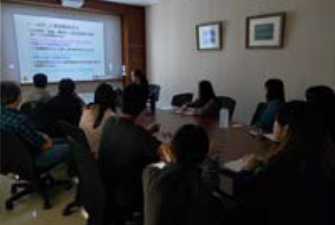
Fire and emergency evacuation training
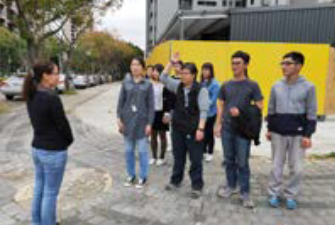
Roll call at a refuge point
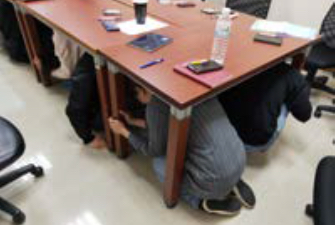
Earthquake drill
Emergency Response Drill for Chemical Leaks in 2019
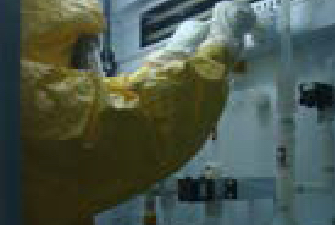
Conducting a drill in chemical operation
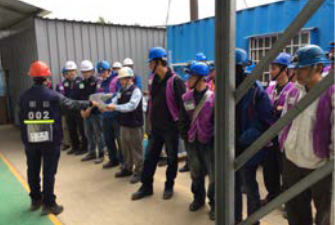
Initiating emergency response and setting up a response team
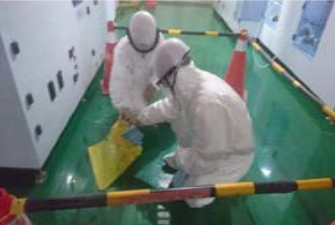
Wearing protective clothing for cleaning
Creating an Accident-Free Workplace
Novatech aims at creating an accident-free workplace. In 2019, each department worked together to achieve the goal of zero industrial accidents, coupled with a certificate of 1,460,721 accident-free hours issued by the Industrial Safety and Health Association (ISHA) of the R.O.C (from September 23, 2014 to June 30, 2019). As of December 31, 2019, we accumulated 1,622,978 accident-free hours. This is manifestation of our respect and dedication to workplace safety over the years. Aiming at building an inclusive and healthy work environment, Novatech has the "Guidelines for Maternity Protection at Work" in place to take care of and protect all female employees of childbearing age (pregnancy or less than one year after childbirth). The "Regulations Governing Prevention of Sexual Harassment and the Guidelines for Prevention of Wrongful Infringement in the Performance of Duties" have also been formulated to provide employees a workplace that is free of sexual harassment and bolsters gender equality.
Type | Employees | Contractors (Workers) | Total | |||
---|---|---|---|---|---|---|
2018 | 2019 | 2018 | 2019 | 2018 | 2019 | |
Total number of working hours | 307,384 | 312,744 | 133,792 | 112,768 | 441,176 | 446,536 |
Disabling injury frequency rate (FR) | 0 | 0 | 0 | 0 | 0 | 0 |
Disabling injury severity rate (SR) | 0 | 0 | 0 | 0 | 0 | 0 |
Frequency severity index (FSI) | 0 | 0 | 0 | 0 | 0 | 0 |
Lost day rate (LDR) | 0% | 0% | 0% | 0% | 0% | 0% |
Absence rate (AR)* - male* | 0.28% | 0.61% | - | - | - | - |
Absence rate (AR)* - female* | 0.23% | 1.96% | - | - | - | - |
The statistics on occupational disasters are based on the key disabling injury indexes announced by the Ministry of Labor, including disabling injury frequency rate (FR), disabling injury severity rate (SR), and absence rate (AR), and exclude traffic accidents outside of Novatech.
Formula:
- Disabling injury frequency rate (FR) = Number of disabling injuries (cases) X 1,000,000 / Total number of working hours
- Disabling injury severity rate (SR) = Number of lost days X 1,000,000 / Total number of working hours
- Lost day rate (LDR) = Total number of lost days / Total number of required working days (Required working days = Total number of working hours / 8 working hours per day, which is consistent with the data declared by the Ministry of Labor)
- Absence rate (AR) = Total number of absent days / Total number of working hours × 100% (Total number of absent days includes occupational sick leave, sick leave, menstrual leave, personal leave, etc.)
Occupational Accident Notification System
The Company completed transition to ISO 45001 in 2018. We have the "Accident Notification and Investigation Management Process" drawn up according to ISO 45001 to implement the accident notification and improvement mechanisms. In accordance with the aforesaid process and local laws and regulations, employees are required to execute the standard operating procedures properly and notify local authorities of occupational accidents within a given time limit, review, investigate and analyze the casualties and property losses arising from EHS incidents on a regular basis, and take and refine necessary precautions to avoid and reduce the possibility of recurrences; the occupational accident notification system is also in place to report occupational accidents level by level according to the statutory requirements. At Novatech, occupational safety is viewed as one of our corporate cultures. In general safety and health training for new employees, the ISEP Department introduces the types of occupational accidents and degree of injury thereof and expects new employees to pay close attention to personal safety and the occupational accident notification system, so as to prevent accidents.
Occupational Safety Training
The Company conducts training strictly according to the "Rules for Occupational Safety and Health Training" to minimize the possibility of occupational disasters. Such training includes "safety and health training for new employees" and "safety and health training for incumbent and transfer employees" for three hours each; operators coming into contact with organic or specialty chemical substances are required to take additional three hours of such training each. Before entering construction sites, all employees and contractors are required to take safety and health training required to perform their work and prevent occupational disasters in accordance with the local laws and regulations or customer requirements, so as to have better understanding of related safety and health regulations; such safety and health training includes "contractor safety and health training" for six hours and "construction site safety training." A toolbox meeting is also held before construction to increase operators' awareness of hazards in the construction sites. The number of EHS training hours in 2019 averaged 4.4 per person.
EHS training hours/person on average in 2019 | ||
---|---|---|
2017 Year Hours | 2018 Year Hours | 2019 Year Hours |
4.1 | 3.2 | 4.4 |
The number of EHS training hours in 2019 averaged 4.4 per person.
Strengthening Contractor Safety and Health Management
Novatech observes the safety and health regulations at home and abroad and customer requirements and takes safe management measures proactively to strengthen employees' and contractors' awareness and responsibility for safety and health. We address ourselves to creating a work environment that helps forward the safety and health of employees and contractors, so as to minimize occupational injuries and disasters. We view contractors as our important business partner. At Novatech, strengthening occupational safety and health in the workplace plays a critical role in contractor management. In 2019, 14,096 contractors undertook construction projects at clients' factories for 112,768 hours. Constant efforts have been made to implement and strengthen the safety awareness of our contractors. The "Contractor Safety Inspection Evaluation Management Process" has been formulated to manage our contractors. According to the aforesaid process, the industrial safety personnel for each project is responsible for asking contractors to abide by the laws and regulations and customer requirements, inspecting and reviewing contractors' safety measures from time to time, and demanding immediate correction upon identifying any defects. This is an effective way to ensure the safety of contractors' employees and to reduce defects identified at clients' factories. In 2019, 49 tickets were issued for improper industrial safety practices and 4 tickets were issued to clients, and no industrial accidents occurred to contractors' employees in the process of carrying out the Company's projects.
Achievements in Occupational Safety and Health Management (Unit: Number) | ||
---|---|---|
Year | Fines Imposed on Clients (Passive Indicator) | Tickets for Industrial Safety Violations (Active Indicator) |
2017 | 2 | 46 |
2018 | 4 | 57 |
2019 | 4 | 49 |
Safety Controls for High-risk Operations
The Company is engaged in the construction of water, gas and chemical related supply equipment pipelines. During the construction period, the Company will encounter many high-risk operations due to the environment or equipment. The "Work Health and Safety Policy" is in place to ensure that employees and contractors are aware of hazards and personal safety during the high-risk operations.
Work Health and Safety Policy
The industrial safety personnel have to be on-the-spot throughout the supervision. If finding that there is any hazard, they should demand immediate shutdown for correction. Construction is only allowed when the industrial safety personnel are on-the-spot. The Company's high-risk operations are as follows:
Type of Operation | Controls |
---|---|
Fall protection | Strengthen the application process and environmental safety facilities, provide qualified protective gear, and promote SOP compliance |
Chemical equipment testing and maintenance | Conduct training and emergency response drills, strengthen the application process and protective gear, and promote SOP compliance, industrial safety personnel monitoring, and chemical waste classification and disposal |
Wiring | Prohibit hotline work, provide qualified protective gear, and promote SOP compliance |
Lifting | Employ qualified contractors and equipment qualified with three certificates, conduct pre-work inspection and work area control (e.g., off-limits under the lifting object), and provide opening protection such as safety belts and fall arrests |
Confined spaces | Set up safety protection plans and hypoxia work supervisors, conduct pre-work training, continuous ventilation, and toxic gas concentration measurement, and strengthen the pre-work application process and reporting before/after work and site manager and industrial safety personnel monitoring, as well as have first responders, protective gear (e.g., respiratory protection, seat belts, and fall arrests) and emergency supplies (SCBA) ready |
Electric welding and acetylene | Strengthen the application process for flame work and on-site safety protection (e.g., fire extinguisher, fire blanket, blackout glasses, and protective gloves), confirm that cylinders are upright and fixed, and put up hazard notices |